Ce troisième volume du « Matériel roulant dans le système ferroviaire » décrit les sous-systèmes embarqués pour faire se mouvoir les trains, les contrôler et les arrêter en toute sécurité. L’ouvrage présente également les locomotives qui les accueillent.
Publier un ouvrage technique qui se veuille la référence auprès des professionnels, et qui puisse aussi combler les attentes des amateurs avertis, est souvent considéré comme la quadrature du cercle. La sortie du troisième tome de la série Matériel roulant dans le système ferroviaire prouve magistralement le contraire. En plagiant une formule bien connue, on pourrait affirmer, sans exagération, que cet ouvrage raconte, avec passion, « tout ce que vous avez toujours rêvé de comprendre sur le fonctionnement d’un train sans jamais avoir osé le demander ». Plus encore que les deux tomes précédents, cette troisième livraison aborde des aspects qui sont à la fois centraux dans toute thématique sur le matériel roulant, mais qui savent également résonner dans l’imaginaire des passionnés. Qu’il s’agisse de la traction électrique ou thermique, des systèmes de freinage, de la conception et des performances des locomotives, de l’agencement des cabines de conduite et de leur ergonomie, ou encore de l’aérodynamique ferroviaire, tous les fondamentaux de la discipline sont ici traités avec l’évident souci de dresser un état de l’art « up-todate », qui puise sa riche illustration dans les réalités du chemin de fer d’aujourd’hui. Qui plus est, le dernier chapitre de l’ouvrage, cette fois résolument prospectif, aborde les perspectives d’avenir promises au matériel roulant. À quoi ressembleront donc les trains de demain ? Si les auteurs, emprunts d’une sage prudence, se gardent bien d’en dessiner trop précisément les contours, ils s’accordent néanmoins à les prédire numériques, intelligents, connectés et automatisés.
On peut leur faire toute confiance. Ce sont des experts de l’industrie ferroviaire, et l’ouvrage a été supervisé, comme à l’accoutumée, par l’incontournable François Lacôte qui, outre ses fonctions successives de directeur du Matériel à la SNCF et de directeur technique chez Alstom, reste probablement le plus éminent spécialiste de la grande vitesse dans le monde. Un soin tout particulier a, par ailleurs, été apporté au choix des photos et des schémas, et la mise en page, particulièrement inventive, rend l’ouvrage aussi attractif à feuilleter que facile à lire, et accessible à qui veut l’approfondir. Édité avec le soutien du mastère spécialisé Systèmes de transports ferroviaires et urbains à destination des élèves ingénieurs et ingénieurs du secteur, il sera très vite un « must » pour tous ceux qui, de près ou de loin, en pincent pour la technologie des trains…
Ph. H.
EXTRAIT 1
Volume, masse et intégration
Dans le cas des locomotives diesels- électriques, le moteur diesel est généralement le composant le plus lourd et le plus volumineux à être installé à bord. De plus il est accouplé au premier élément de la transmission de puissance à savoir l’alternateur, et ce groupe électrogène représente un ensemble encore plus volumineux et plus lourd. Pour équilibrer convenablement la locomotive, le groupe électrogène doit être placé autant que possible au centre de la locomotive.
Ce requis est également valable pour le réservoir de gazole dont la masse varie de plusieurs tonnes suivant qu’il est vide ou plein.
Cette contrainte pousse à disposer le groupe électrogène et le réservoir dans la même section, tout en respectant les contraintes de masse à l’essieu propres au réseau sur lequel devra rouler la locomotive. La figure 38 ci-dessous donne un exemple d’installation des principaux éléments d’une locomotive diesel-électrique et le tableau de la figure 39 ci-dessous propose un bilan de masse de l’ensemble du système de génération d’énergie.
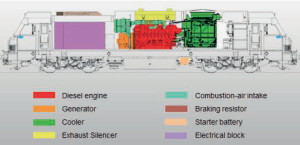
Fig. 38 : intégration d’un groupe électrogène dans une locomotive diesel-électrique (Alstom).
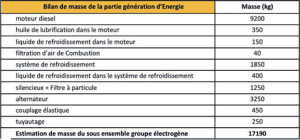
Fig. 39 : bilan de masse des composants du système de génération d’énergie.
Pour une locomotive diesel- hydraulique, l’équilibrage et l’intégration sont encore moins aisés. En effet, la boîte hydraulique, entraînée elle-même par l’arbre du moteur, entraîne simultanément les mécanismes de propulsion situés dans les bogies.
La boîte doit donc être disposée en position médiane, ce qui impose de décentrer moteur Diesel doit être décentrée et le réservoir de gazole doit être divisé longitudinalement en deux compartiments, afin de laisser le passage aux arbres d’entraînement liant la boit aux bogies (voir figure 40 ci-dessous).

Fig. 40 : intégration d’un système de traction diesel-hydraulique dans une locomotive de manoeuvre (Vossloh).
1. moteur diesel
2. boîte hydraulique
3. réducteur
4. turbine de refroidissement
5. radiateurs
6. silencieux d’échappement
7. filtre à air
8. réservoir de gazole
9. armoire frein
10. réservoir d’air & compresseur
11. batteries
12. sablière
Cas des autorails et des automotrices
Les premiers éléments automoteurs modernes étaient équipés d’un seul moteur industriel puissant, monté en caisse, mais la nécessité d’augmenter la capacité en passagers a poussé les constructeurs à reloger le moteur diesel à l’extérieur de l’habitacle du véhicule. De plus, l’utilisation de moteurs de plus faible puissance, car plus petits, a rendu nécessaire l’installation de plusieurs moteurs par rame automotrice, suivant le niveau de puissance de traction. De nos jours, les « Power packs » sont montés sous caisse ou en toiture. Le terme Power-pack désigne l’ensemble constitué par le moteur diesel et l’alternateur en transmission électrique, ou la boîte de vitesses en transmission hydromécanique. Le tout est intégré dans un châssis propre au Power pack. Dans les conceptions les plus compactes, le Power pack inclut également le système de refroidissement du moteur diesel et peut être considéré comme une véritable centrale électrique autonome, apportant son énergie au système de traction du véhicule ainsi qu’aux systèmes auxiliaires de chauffage, ventilation et climatisation (HVAC) et autres.
Intégration en caisse
Certains autorails anciens étaient équipés de moteurs diesels identiques aux moteurs de locomotives, ce qui imposait une intégration en caisse.
La puissance de leur moteur permettait de tracter des remorques et d’assurer un service sur des lignes escarpées de montagne. En plus du compartiment moteur, un espace était réservé aux bagages et aux marchandises.
L’ensemble de ces deux espaces occupait le tiers de l’espace disponible dans la caisse du véhicule (voir figures 41 à 43 ci-dessous).
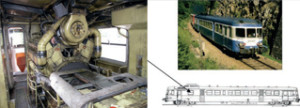
Fig. 41 à 43 : intégration en caisse d’un moteur SACM MGO V12 de 607 kW dans un autorail SNCF X 2800 (SNCF).
Disposition sous caisse
L’intégration sous caisse fut la première étape dans la conception de nouvelles rames automotrices pour gagner de l’espace pour les passagers et augmenter le nombre de places assises. Le système de propulsion fut d’abord constitué d’un moteur diesel couplé à une boîte de vitesses hydromécanique, d’arbres de transmission à cardan et de réducteurs, pour réaliser la liaison avec les roues. Plus tard, des Power packs électriques furent également disposés sous caisse. Il arrivait toutefois que ce type de conception oblige les passagers à gravir des marches supplémentaires pour monter à bord du véhicule (voir figures 44 à 46 ci-dessous).
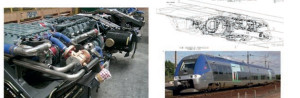
Fig. 44 à 46 : intégration sous caisse d’un Power pack de 662 kW sur un EAM SNCF X 76500 (Bombardier).
Disposition en toiture
Un avantage de la traction diesel- électrique par rapport à un système de traction hydromécanique conventionnel, est qu’elle permet de disposer le Power pack en toiture et de distribuer l’énergie électrique au moyen de câbles électriques de puissance. Ceci engendre toutefois de nouveaux problèmes techniques, par exemple l’alimentation en gazole en provenance du réservoir situé sous caisse, ou la purge d’air du système de refroidissement du moteur, puisque les radiateurs ou le moteur sont aussi hauts que le vase d’expansion. Mais cette disposition permet d’abaisser le niveau du plancher des véhicules pour un meilleur confort des voyageurs (voir figures 47 à 49 ci-dessous).
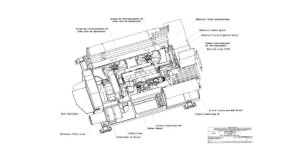
Fig. 47 : disposition en
toiture de deux Power
packs sur une
automotrice Régiolis
SNCF B 83500
(Alstom).
EXTRAIT 2
Compléments sur le sujet de l’aérodynamique ferroviaire
Introduction
Quelle est l’importance de l’aérodynamique pour la conception, le dimensionnement et l’exploitation des systèmes ferroviaires ? Pourquoi existe-t-il des exigences aérodynamiques pour les véhicules ? Quels sont les critères qui ont guidé le choix des exigences et de leurs limites telles qu’on peut les trouver aujourd’hui notamment dans la STI LOC & PAS ?
Il nous a semblé nécessaire, à la fin de cet ouvrage, de revenir plus en détail sur ces questions qui ont déjà été abordées partiellement au chapitre consacré aux trains à grande et très grande vitesse. Des problèmes d’aérodynamique se posent en effet pour la conception de tous types de matériel, pour voyageurs et pour marchandises.
L’aérodynamique influence la conception de presque tous les sous-systèmes embarqués, qu’il s’agisse de confort (bruit, confort tympanique, etc.), de structures de caisse ou de systèmes de portes qui doivent résister aux efforts alternés générés par les ondes de pression, de performances de traction ou de questions de sécurité à l’interface avec l’infrastructure ferroviaire (vents traversiers, projections de ballast, effets de souffle etc.). Ce chapitre fournit quelques informations scientifiques et contextuelles et propose une interprétation des exigences réglementaires et normatives.
L’amélioration des performances aérodynamiques fut une des préoccupations majeures des concepteurs de matériel roulant dès les années 1920-1930, quand il apparut que la puissance relativement faible des machines à vapeur ne permettrait l’obtention de vitesses supérieures qu’en rationalisant la forme des locomotives.
Les deux « Stromlinienlokomotiven » construites par Borsig Werke à Berlin en 1935 pour rouler à 175 km/h en sont un bon exemple (figure 1 ci-dessous), l’une d’elles ayant atteint le 11 mai 1936 la vitesse de 200,4 km/h.
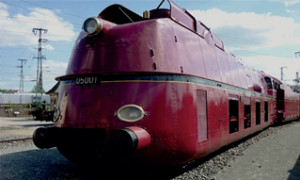
Fig. 1 : locomotive à vapeur BR05 de la Deutsche Reichsbahn, optimisée du point de vue aérodynamique, (dbmuseum.de).
Les développements de la traction électrique pendant le XXe siècle permirent une forte hausse de la puissance disponible pour la transmission d’effort aux rails, et réduisirent l’exigence d’une conception aérodynamique des matériels roulants, les conséquences défavorables de leur style médiocre étant largement compensée par l’augmentation de puissance.
C’est seulement avec l’avènement des trains à très grande vitesse Shinkansen, puis TGV et ICE que l’aérodynamique ferroviaire fit son retour en tant que discipline d’ingénierie, et comme sujet majeur de recherche pour les ingénieurs ferroviaires. La performance aérodynamique fut l’un des aspects les plus importants pour la conception des AGV d’Alstom (figure 2 ci-dessous)
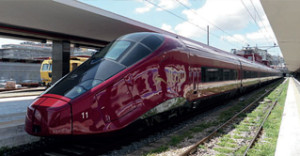
Fig. 2 : automotrice à très grande vitesse AGV d’Alstom (Italo Napoli).
La famille Zefiro de Bombardier (figure 3 ci-dessous) a également fait l’objet d’une optimisation aérodynamique.

Fig. 3 : train à grande vitesse Zefiro de Bombardier (Bombardier).
Un autre élément déclencheur des études aérodynamiques a été la génération d’ondes de pression en tunnel, dont le niveau augmente avec le carré de la vitesse et qui entraînent une gêne auditive dans le cas des trains non étanches à la pression, mais aussi des contraintes élevées sur les structures et également un effet de « bang supersonique » à l’extrémité du tunnel. La nécessité de réduire l’effet de « bang supersonique » entraîne également des modifications dans la construction des tunnels.
Ces mesures pour les infrastructures comprennent l’installation de protections soniques à l’entrée du tunnel et de murs perforés permettant d’amortir la variation de pression à la sortie.
Les lignes ferroviaires à grande vitesse japonaises en particulier présentent des diamètres de tunnel relativement faibles, entraînant des ratios de blocage élevés. Ceci a donné lieu à une optimisation particulière de la tête du train, par exemple celle du Shinkansen N700 (figure 4 ci-dessous). Le principe de conception de ces formes allongées est d’augmenter le maître couple le long du nez de façon aussi lente et régulière que possible.
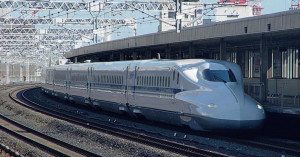
Fig. 4 : rame Shinkansen N700 japonaise avec géométrie frontale spéciale pour réduire l’effet du bang supersonique (Wikipedia).
Cela permet de limiter le gradient de pression dont dépend l’amplitude du bang supersonique.
Cliquez sur la couverture pour vous procurer ce livre disponible sur notre site internet :
Cliquez sur les couvertures du Tome 1 et du Tome 2 s’il vous les manque pour avoir la collection complète :